API 510 remaining life: Half-Life VS Double Corrosion Rate principles
One of the first objectives of an in-service inspection of pressure vessels is to estimate the remaining life and to set the next planned internal and external intervals. API 510 gives guidance on how to calculate these parameters.
At first look, it seems just a matter of a simple equation where remaining life can be calculated known as the corrosion rate, the current thickness, and the retirement thickness. In the API exam certainly, it is not a complicated question to be answered as in most cases all these parameters are given.
But in reality, it is far more than that. For example, the corrosion rate is not given and the authorized inspector shall estimate it. If erroneous the result of the inspection will be also. Here it is a question of understanding the whole approach rather than just giving a result of an equation. The authorized inspector has the responsibility to pronounce the Vessel’s state. Is it fit to serve? For how long? When the next inspection shall be conducted? Are there any safety issues? Is NDT well performed? Are the NDT results acceptable? Are there any repairs to be performed before start-up?
Many other questions can arise but basically, in terms of remaining life calculation the most important question to be answered by the order are the following:
- What approach shall be used when calculating the remaining life (Half-Life or Double Corrosion rate?
- Is the corrosion rate adopted correct and reflects the real state of the vessel?
We will try in this article to answer these two questions and detail also some other aspects to be considered when evaluating the remaining life (aspects that API 510 does not clearly explain but are rules of thumb).
I Half-Life VS Double Corrosion Rate principles
I-1 Half-Life principle
If you are an authorized API 510 inspector or intend to sit for the API 510 exam, you must know the Half-life principle adopted by API 510 for setting the internal inspection intervals of in-service pressure vessels. The principle is easy to understand:
- Calculate the remaining life of the vessel knowing the corrosion rate, the actual thickness, and the retirement thickness (trequired)
\frac{t_{actual} – t_{required}}{corrosion rate}
- The Internal inspection interval will be the half remaining life but shall not exceed 10 years
- Exceptions for vessels of the remaining life of 04 years and less where internal inspection interval is set to the hole remaining life but not exceeding 02 Years
For the last point, is it complicated? To simplify, it means that if the remaining life is between 04 and 02 years the inspection interval is 02 years otherwise for vessels with a remaining life of fewer than 02 years the inspection interval is equal to the whole remaining life. For instance, a vessel with a remaining life of 01 year shall be inspected internally after 01 years.
Personally, at the time when I was preparing for the API 510 exams, I found that this last point is counterintuitive. How we can tolerate that a pressure vessel will serve up to its whole remaining life before conducting an inspection? Would it not be risky?
Since then, I was searching for the reason for this mysterious clause. In the end, the only explanation that convinced me is that API 510 and other API standards; in many of its clauses; are based on owners’ feedback rather than empirical static formulas. That is why the API committee is one of the largest committees in the field of standardization. This rule was tested successfully for tens of years and no need to reinvent the wheel. This success may be related to the fact that construction codes adopts always a safety factor. For example in ASME VIII division 1, for tensile strength, the code requires a safety factor of 3,5. ASME BPV Section VIII, Division 2, uses a much smaller safety factor on tensile strength than Division 1 does. The safety factor is 2,4 instead.
Here it means that the required thickness is calculated not based on the actual material tensile strength but on lesser allowable stress. Hence giving a safety margin that API 510 is using to allow such a clause. This is surely a temporary measure to give owners and users more time for more radical solutions as it is clear that shutting down pressure vessels at very short intervals seems more expensive.
I-2 Double Corrosion Rate principle
to use it or even do not understand it well.
In reality, it is the same thing as the previous approach but here based on the iterative calculation of the maximum allowable Pressure. In the end, the results of the two methods are approximately the same. But the double corrosion rate principle gives a more accurate result.
When using this approach the inspector shall be careful to correct the inner radius by 2 times the corrosion rate. Actually, the inner diameter tends to be larger over time.
By correcting initially the thickness and the inner radius considering 02 times the corrosion rate the result will be automatically the remaining life/2 .
We will try to illustrate this approach via an example so the whole picture gets clearer
.
Below is an example of a pressure Vessel Parameter:
Symbol | Variable | Value |
---|---|---|
Di | Initial Internal Diameter | 96 In |
Ri | Initial Internal Radius | 48 In |
torg | Original Thickness | 1.25 In |
tcr | Current Thickness | 0.92 In |
S | Allowable Stress | 16250 psi |
E | Joint Efficiency | 1 |
CR | Corrosion rate | 0.001 In/year |
tr | Retirement Thickness | 0.896 In |
MAWPr | Retirement MAWP | 300 psi |
Maximum allowable Pressure as a function of time is given by the below formula. You can see that the ASME formula for calculating MAWP is now corrected by subtracting 2 times the corrosion rate from the thickness and adding 2 times the corrosion rate to the inside radius. Where I is the incrimination of time interval since the inspection date
MAWP(t) = \frac{S*E*tcr – 2*CR*I}{R_{i} + 2*CR*I + 0.6 *(tcr-2*CR*I)}
Iterations give us the following result:
l | tcr-2*cr*I | Ri +2 *CR*I | MAWP(t) | MAWPr |
---|---|---|---|---|
0 | 0.92 | 48 | 307.9172846 | 300 |
0.1 | 0.9198 | 48.0002 | 307.8498388 | 300 |
0.2 | 0.9196 | 48.0004 | 307.7823932 | 300 |
0.3 | 0.9194 | 48.0006 | 307.7149479 | 300 |
0.4 | 0.9192 | 48.0008 | 307.6475027 | 300 |
0.5 | 0.919 | 48.001 | 307.5800578 | 300 |
0.6 | 0.9188 | 48.0012 | 307.5126132 | 300 |
0.7 | 0.9186 | 48.0014 | 307.4451687 | 300 |
0.8 | 0.9184 | 48.0016 | 307.3777245 | 300 |
0.9 | 0.9182 | 48.0018 | 307.3102805 | 300 |
1 | 0.918 | 48.002 | 307.2428367 | 300 |
1.1 | 0.9178 | 48.0022 | 307.1753931 | 300 |
1.2 | 0.9176 | 48.0024 | 307.1079498 | 300 |
1.3 | 0.9174 | 48.0026 | 307.0405066 | 300 |
1.4 | 0.9172 | 48.0028 | 306.9730637 | 300 |
1.5 | 0.917 | 48.003 | 306.9056211 | 300 |
1.6 | 0.9168 | 48.0032 | 306.8381786 | 300 |
1.7 | 0.9166 | 48.0034 | 306.7707364 | 300 |
1.8 | 0.9164 | 48.0036 | 306.7032943 | 300 |
1.9 | 0.9162 | 48.0038 | 306.6358526 | 300 |
2 | 0.916 | 48.004 | 306.568411 | 300 |
2.1 | 0.9158 | 48.0042 | 306.5009696 | 300 |
2.2 | 0.9156 | 48.0044 | 306.4335285 | 300 |
2.3 | 0.9154 | 48.0046 | 306.3660876 | 300 |
2.4 | 0.9152 | 48.0048 | 306.2986469 | 300 |
2.5 | 0.915 | 48.005 | 306.2312065 | 300 |
2.6 | 0.9148 | 48.0052 | 306.1637663 | 300 |
2.7 | 0.9146 | 48.0054 | 306.0963262 | 300 |
2.8 | 0.9144 | 48.0056 | 306.0288865 | 300 |
2.9 | 0.9142 | 48.0058 | 305.9614469 | 300 |
3 | 0.914 | 48.006 | 305.8940075 | 300 |
3.1 | 0.9138 | 48.0062 | 305.8265684 | 300 |
3.2 | 0.9136 | 48.0064 | 305.7591295 | 300 |
3.3 | 0.9134 | 48.0066 | 305.6916908 | 300 |
3.4 | 0.9132 | 48.0068 | 305.6242524 | 300 |
3.5 | 0.913 | 48.007 | 305.5568142 | 300 |
3.6 | 0.9128 | 48.0072 | 305.4893761 | 300 |
3.7 | 0.9126 | 48.0074 | 305.4219384 | 300 |
3.8 | 0.9124 | 48.0076 | 305.3545008 | 300 |
3.9 | 0.9122 | 48.0078 | 305.2870634 | 300 |
4 | 0.912 | 48.008 | 305.2196263 | 300 |
4.1 | 0.9118 | 48.0082 | 305.1521894 | 300 |
4.2 | 0.9116 | 48.0084 | 305.0847527 | 300 |
4.3 | 0.9114 | 48.0086 | 305.0173163 | 300 |
4.4 | 0.9112 | 48.0088 | 304.9498801 | 300 |
4.5 | 0.911 | 48.009 | 304.882444 | 300 |
4.6 | 0.9108 | 48.0092 | 304.8150083 | 300 |
4.7 | 0.9106 | 48.0094 | 304.7475727 | 300 |
4.8 | 0.9104 | 48.0096 | 304.6801373 | 300 |
4.9 | 0.9102 | 48.0098 | 304.6127022 | 300 |
5 | 0.91 | 48.01 | 304.5452673 | 300 |
5.1 | 0.9098 | 48.0102 | 304.4778326 | 300 |
5.2 | 0.9096 | 48.0104 | 304.4103982 | 300 |
5.3 | 0.9094 | 48.0106 | 304.342964 | 300 |
5.4 | 0.9092 | 48.0108 | 304.2755299 | 300 |
5.5 | 0.909 | 48.011 | 304.2080962 | 300 |
5.6 | 0.9088 | 48.0112 | 304.1406626 | 300 |
5.7 | 0.9086 | 48.0114 | 304.0732292 | 300 |
5.8 | 0.9084 | 48.0116 | 304.0057961 | 300 |
5.9 | 0.9082 | 48.0118 | 303.9383632 | 300 |
6 | 0.908 | 48.012 | 303.8709305 | 300 |
6.1 | 0.9078 | 48.0122 | 303.8034981 | 300 |
6.2 | 0.9076 | 48.0124 | 303.7360658 | 300 |
6.3 | 0.9074 | 48.0126 | 303.6686338 | 300 |
6.4 | 0.9072 | 48.0128 | 303.601202 | 300 |
6.5 | 0.907 | 48.013 | 303.5337705 | 300 |
6.6 | 0.9068 | 48.0132 | 303.4663391 | 300 |
6.7 | 0.9066 | 48.0134 | 303.398908 | 300 |
6.8 | 0.9064 | 48.0136 | 303.3314771 | 300 |
6.9 | 0.9062 | 48.0138 | 303.2640464 | 300 |
7 | 0.906 | 48.014 | 303.196616 | 300 |
7.1 | 0.9058 | 48.0142 | 303.1291857 | 300 |
7.2 | 0.9056 | 48.0144 | 303.0617557 | 300 |
7.3 | 0.9054 | 48.0146 | 302.9943259 | 300 |
7.4 | 0.9052 | 48.0148 | 302.9268964 | 300 |
7.5 | 0.905 | 48.015 | 302.859467 | 300 |
7.6 | 0.9048 | 48.0152 | 302.7920379 | 300 |
7.7 | 0.9046 | 48.0154 | 302.724609 | 300 |
7.8 | 0.9044 | 48.0156 | 302.6571803 | 300 |
7.9 | 0.9042 | 48.0158 | 302.5897519 | 300 |
8 | 0.904 | 48.016 | 302.5223236 | 300 |
8.1 | 0.9038 | 48.0162 | 302.4548956 | 300 |
8.2 | 0.9036 | 48.0164 | 302.3874678 | 300 |
8.3 | 0.9034 | 48.0166 | 302.3200403 | 300 |
8.4 | 0.9032 | 48.0168 | 302.2526129 | 300 |
8.5 | 0.903 | 48.017 | 302.1851858 | 300 |
8.6 | 0.9028 | 48.0172 | 302.1177589 | 300 |
8.7 | 0.9026 | 48.0174 | 302.0503322 | 300 |
8.8 | 0.9024 | 48.0176 | 301.9829058 | 300 |
8.9 | 0.9022 | 48.0178 | 301.9154795 | 300 |
9 | 0.902 | 48.018 | 301.8480535 | 300 |
9.1 | 0.9018 | 48.0182 | 301.7806277 | 300 |
9.2 | 0.9016 | 48.0184 | 301.7132022 | 300 |
9.3 | 0.9014 | 48.0186 | 301.6457768 | 300 |
9.4 | 0.9012 | 48.0188 | 301.5783517 | 300 |
9.5 | 0.901 | 48.019 | 301.5109268 | 300 |
9.6 | 0.9008 | 48.0192 | 301.4435021 | 300 |
9.7 | 0.9006 | 48.0194 | 301.3760776 | 300 |
9.8 | 0.9004 | 48.0196 | 301.3086534 | 300 |
9.9 | 0.9002 | 48.0198 | 301.2412294 | 300 |
10 | 0.9 | 48.02 | 301.1738056 | 300 |
10.1 | 0.8998 | 48.0202 | 301.106382 | 300 |
10.2 | 0.8996 | 48.0204 | 301.0389587 | 300 |
10.3 | 0.8994 | 48.0206 | 300.9715356 | 300 |
10.4 | 0.8992 | 48.0208 | 300.9041127 | 300 |
10.5 | 0.899 | 48.021 | 300.83669 | 300 |
10.6 | 0.8988 | 48.0212 | 300.7692675 | 300 |
10.7 | 0.8986 | 48.0214 | 300.7018453 | 300 |
10.8 | 0.8984 | 48.0216 | 300.6344233 | 300 |
10.9 | 0.8982 | 48.0218 | 300.5670015 | 300 |
11 | 0.898 | 48.022 | 300.4995799 | 300 |
11.1 | 0.8978 | 48.0222 | 300.4321586 | 300 |
11.2 | 0.8976 | 48.0224 | 300.3647374 | 300 |
11.3 | 0.8974 | 48.0226 | 300.2973165 | 300 |
11.4 | 0.8972 | 48.0228 | 300.2298959 | 300 |
11.5 | 0.897 | 48.023 | 300.1624754 | 300 |
11.6 | 0.8968 | 48.0232 | 300.0950552 | 300 |
11.7 | 0.8966 | 48.0234 | 300.0276351 | 300 |
11.8 | 0.8964 | 48.0236 | 299.9602153 | 300 |
11.9 | 0.8962 | 48.0238 | 299.8927958 | 300 |
12 | 0.896 | 48.024 | 299.8253764 | 300 |
This can be illustrated graphically as in the below figure
The vessel’s Half remaining life is 11.7 Years (Versus 12 years if based on the thickness approach) which means that the next planned inspection shall be in 10 years.
In terms of results, there are no big differences between the two approaches but in terms of information, the second approach is very illustrative. In fact, the above figure constitutes the modeling of a pressure safety envelope up to the end of the vessel life if the corrosion rate remains the same. This can be also corrected if additional on-stream thickness measurements are conducted at regular intervals.
I-3 Half-Life or Double Corrosion Rate principles which one to use?
In general, there are no rules. The two approaches give correct results. The first approach based on thicknesses is a quick conservative tool. The second one based on the iterative calculation of MAWP is a more detailed method with more accurate results and a more useful output. There is a case where API 510 gives reference to the Double Corrosion Rate principle.
When the pressure vessel is working in corrosive service, API 510 advises correcting the thickness by considering double the corrosion rate. API 510 does not explicitly state to calculate the remaining life by this method but rather the MAWP but in the end, it is the same thing.
If we consider the same example as the one stated previously, but with the vessel working in corrosive service we will have the following (after correcting the thickness and the inner Radius by 4 times the corrosion rate:
l | tcr-2*cr*I | Ri +2 *CR*I | MAWP(t) | MAWPr |
---|---|---|---|---|
0 | 0.92 | 48 | 307.9172846 | 300 |
0.1 | 0.9196 | 48.0004 | 307.7823932 | 300 |
0.2 | 0.9192 | 48.0008 | 307.6475027 | 300 |
0.3 | 0.9188 | 48.0012 | 307.5126132 | 300 |
0.4 | 0.9184 | 48.0016 | 307.3777245 | 300 |
0.5 | 0.918 | 48.002 | 307.2428367 | 300 |
0.6 | 0.9176 | 48.0024 | 307.1079498 | 300 |
0.7 | 0.9172 | 48.0028 | 306.9730637 | 300 |
0.8 | 0.9168 | 48.0032 | 306.8381786 | 300 |
0.9 | 0.9164 | 48.0036 | 306.7032943 | 300 |
1 | 0.916 | 48.004 | 306.568411 | 300 |
1.1 | 0.9156 | 48.0044 | 306.4335285 | 300 |
1.2 | 0.9152 | 48.0048 | 306.2986469 | 300 |
1.3 | 0.9148 | 48.0052 | 306.1637663 | 300 |
1.4 | 0.9144 | 48.0056 | 306.0288865 | 300 |
1.5 | 0.914 | 48.006 | 305.8940075 | 300 |
1.6 | 0.9136 | 48.0064 | 305.7591295 | 300 |
1.7 | 0.9132 | 48.0068 | 305.6242524 | 300 |
1.8 | 0.9128 | 48.0072 | 305.4893761 | 300 |
1.9 | 0.9124 | 48.0076 | 305.3545008 | 300 |
2 | 0.912 | 48.008 | 305.2196263 | 300 |
2.1 | 0.9116 | 48.0084 | 305.0847527 | 300 |
2.2 | 0.9112 | 48.0088 | 304.9498801 | 300 |
2.3 | 0.9108 | 48.0092 | 304.8150083 | 300 |
2.4 | 0.9104 | 48.0096 | 304.6801373 | 300 |
2.5 | 0.91 | 48.01 | 304.5452673 | 300 |
2.6 | 0.9096 | 48.0104 | 304.4103982 | 300 |
2.7 | 0.9092 | 48.0108 | 304.2755299 | 300 |
2.8 | 0.9088 | 48.0112 | 304.1406626 | 300 |
2.9 | 0.9084 | 48.0116 | 304.0057961 | 300 |
3 | 0.908 | 48.012 | 303.8709305 | 300 |
3.1 | 0.9076 | 48.0124 | 303.7360658 | 300 |
3.2 | 0.9072 | 48.0128 | 303.601202 | 300 |
3.3 | 0.9068 | 48.0132 | 303.4663391 | 300 |
3.4 | 0.9064 | 48.0136 | 303.3314771 | 300 |
3.5 | 0.906 | 48.014 | 303.196616 | 300 |
3.6 | 0.9056 | 48.0144 | 303.0617557 | 300 |
3.7 | 0.9052 | 48.0148 | 302.9268964 | 300 |
3.8 | 0.9048 | 48.0152 | 302.7920379 | 300 |
3.9 | 0.9044 | 48.0156 | 302.6571803 | 300 |
4 | 0.904 | 48.016 | 302.5223236 | 300 |
4.1 | 0.9036 | 48.0164 | 302.3874678 | 300 |
4.2 | 0.9032 | 48.0168 | 302.2526129 | 300 |
4.3 | 0.9028 | 48.0172 | 302.1177589 | 300 |
4.4 | 0.9024 | 48.0176 | 301.9829058 | 300 |
4.5 | 0.902 | 48.018 | 301.8480535 | 300 |
4.6 | 0.9016 | 48.0184 | 301.7132022 | 300 |
4.7 | 0.9012 | 48.0188 | 301.5783517 | 300 |
4.8 | 0.9008 | 48.0192 | 301.4435021 | 300 |
4.9 | 0.9004 | 48.0196 | 301.3086534 | 300 |
5 | 0.9 | 48.02 | 301.1738056 | 300 |
5.1 | 0.8996 | 48.0204 | 301.0389587 | 300 |
5.2 | 0.8992 | 48.0208 | 300.9041127 | 300 |
5.3 | 0.8988 | 48.0212 | 300.7692675 | 300 |
5.4 | 0.8984 | 48.0216 | 300.6344233 | 300 |
5.5 | 0.898 | 48.022 | 300.4995799 | 300 |
5.6 | 0.8976 | 48.0224 | 300.3647374 | 300 |
5.7 | 0.8972 | 48.0228 | 300.2298959 | 300 |
5.8 | 0.8968 | 48.0232 | 300.0950552 | 300 |
5.9 | 0.8964 | 48.0236 | 299.9602153 | 300 |
The Half Remaining life is estimated to 5,8 Years, thus the next internal inspection shall be in 5,8 years not 10 years as previously stated for non-corrosive service.
So personally I consider Double Corrosion Rate approach more adequate for authorized inspectors to adopt.
II Corrosion Rate Selection:
In reality, the remaining life calculation method is not as critical as the corrosion rate calculation and selection. The use of an erroneous corrosion rate will automatically impact the inspection result.
To make sure that the calculated corrosion rate is correct the authorized inspector shall check the following:
- Consult with operation personnel and if required with a corrosion specialist to check if the vessel was subject to change in service and or design in the past that can affect the corrosion rate.
- Analyze statistically the thickness measurement records to characterize internal thinning.
- Apply the principle of API 510 section 7 when conducting averaging of the thickness readings or the principle of thickness profiling stated in API 579 part 5.
II-1 Effect of Service/Design Change on Corrosion rate selection
API 510 defines two types of Corrosion rates to be used Short Term Corrosion rate and Long Term Corrosion Rate. It is a very simplistic approach to state that the higher of these two rates shall be used.
For instance, a change in the process can affect the corrosion rate by increasing or decreasing it. The approximate date of such change shall be estimated via consulting with operation personnel. Such an event can be suspected if a notable change in the corrosion rate tendency is observed from previous inspection reports. If confirmed the long-term corrosion rate shall be calculated from that date of service change.
The changing of a pressure vessel part material of construction is also the essential information to be gathered and checked otherwise inaccurate results will be generated.
II-2 Statistical analysis of Thickness Measurement
One of the most efficient ways (of course after visual inspection) to identify the type of internal thinning is by analyzing the result of thickness measurements statistically.
As a rule of thumb, If the COV of the thickness reading population minus the Future Corrosion Allowance (FCA) is less than 10%, then the general metal loss is defined to be uniform and the average thickness can be computed directly from the population of thickness readings.
If the COV is greater than 10%, then the use of thickness profiles is required to determine the average thickness. API 510 gives many criteria on how to average localized thinned areas.
If the COV test for point thickness readings is greater than 10%, then the general metal loss is defined to be non-uniform and the use of thickness profiles is required. An inspection grid covering the region of metal loss is typically required to determine the extent of the damage.
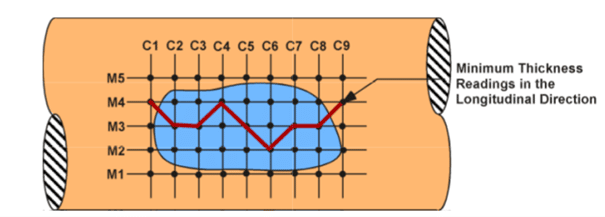
In the end, what I wanted to say here is that corrosion rate selection and related remaining life calculation is a critical activity that API 510 inspectors shall not neglect. Inspectors shall have a solid understanding of their choices and estimations.
There are many other related topics that can be discussed also here but I prefer to detail them in other articles.
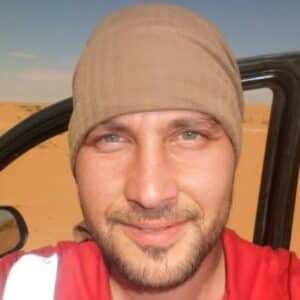
Ali Sassi
If you have any API 510 questions do not hesitate to contact us.
we offer also API 510 training sessions to prepare candidates to pass the API exam with our partner WTC. If you would like to learn more visit http://www.wtctunisie.com